Week 6
- Tessa Wishart
- Aug 24, 2021
- 14 min read
Updated: Sep 16, 2021
17th - 23rd August
Previously Due
(Slightly delayed timeline but trying to catch up) -
One Final Garment. (As this would have to be a primary garment I was hoping to have made either my skirt/dress OR my denim jacket, particularly given how the jacket is designed to be loose fitting and casually dress down a dressy garment/undergarment - I could get away without an official model fitting and fit on someone else instead for better time economies.
Two fully toiled looks (Personally would've tried for at least first toiles or close to final toiles.)
Better more full development of my range plan as dictated by zero waste possibilities.
Lockdown
A weekly analysis -
My week started off with handing in my (extended timeline) Design Proposal on Tuesday 17th. At this time, I'd purchased only a small range of fabrics and I'd developed two first toiles; one primary and one secondary. Unfortunately, on the evening of the Tuesday the country was announced to be going into a Level 4 lockdown of at least 7 days, with any possible length of extended timeline beyond that. I managed to collect all of the equipment that I have to work from home, but won't have access to much drafting paper, and won't be able to purchase any extra fabrics I need until at least level 3 for online or level 2 for in personal - a week away at the absolute least.
This does lead me to need to consider what changes due to lockdown may need to be made. At this stage in the timeline, with about seven weeks to go, I'm really hoping to be able to adhere to my current proposal concept with it's strict sustainability processes and timeline formats. However, the limitation of this waste management concept is that even though I do have some final fabrics, I can't work out of order at all without creating less waste than intended, so I may not be able to make many garments at all. If I do find lockdown to be extending for too long I may have to relax this concept slightly, but do hope to be able to stick to it at this stage.
The more pressing concern for me is the lack of access to facilities - particularly the print lab facility which I need to use to create my printwork pieces and etching for any etched metalwork. What this means for me is that A) garments designed with metalwork hardware will be missing key components if I can't manufacture them; and B) fabrics which need to be flat printed can't be done so without access, so I won't be able to construct those garments until I'm able to print the fabric. (Majority of garments should be printed before construction and it's less possible and a lot more risky to do so after. )

A mood map of how I may use time to develop some visual sources for use in my final prints! Being at home may give me better access and availability for this.
It may be really nice to develop at least one:
- Colour Print in blocks of Layering (Tracing Paper?)
- Textured Monochrome Oil Painting for Printing
- Linework Image(s)
- Lots of designs/source material to use for making my etched buckles! Little drawings of nude ladies etc.
I should also consider developing patterns and repeating patterns etc. Something which worked really well in my last minor work was collaging together smaller pieces of imagery to the the acetate cyanotype printing layers based on the shape of each final garment pattern piece, as opposed to deliberately going to the trouble of making a repeating pattern given how I'm best at working in a more analogue based process style.

Holly McQuillan Screen Printing - Feeding into Range Lineup
Something that stands out in Holly McQuillan's Make/Use collection is how the zero waste pieces are designed as digital prints or screen prints with the patterns pre printed on. The fact that I'm thinking to design at least on Primary zero waste garment which is largely printed means that I could use a printing process to apply the same technique of making in both a visual pattern or design, as well as the actual cut lines of the pattern. Given how much I value to processes of my own work as a handcrafter, I also think that seamwork and linework and illumination and the view of the joins and inside of seams can be so so interesting as a detail which is illuminated to the wearer or viewer.
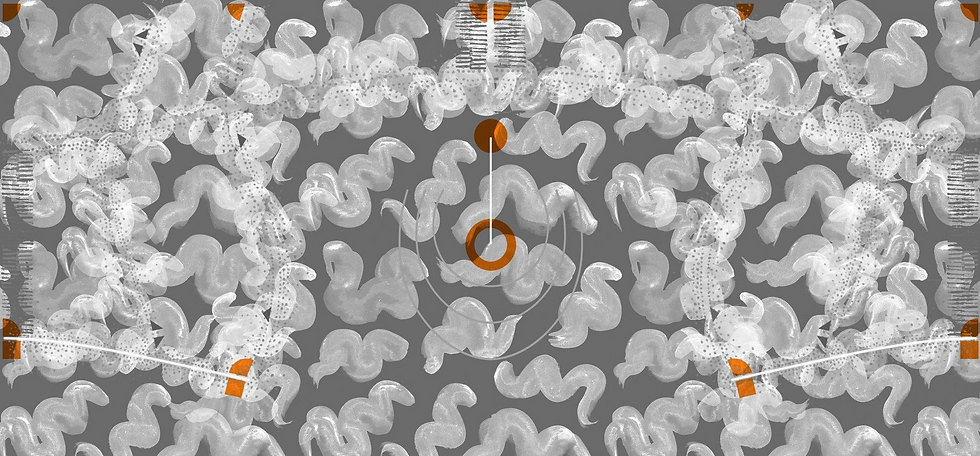
McQuillan Make/Use Wrap Dress Print Layout - Especially love the orange 'notches' which show up as features on the dress but also dictate areas for joining.
A note on mixing or blending fabric types (and colours) in designs?
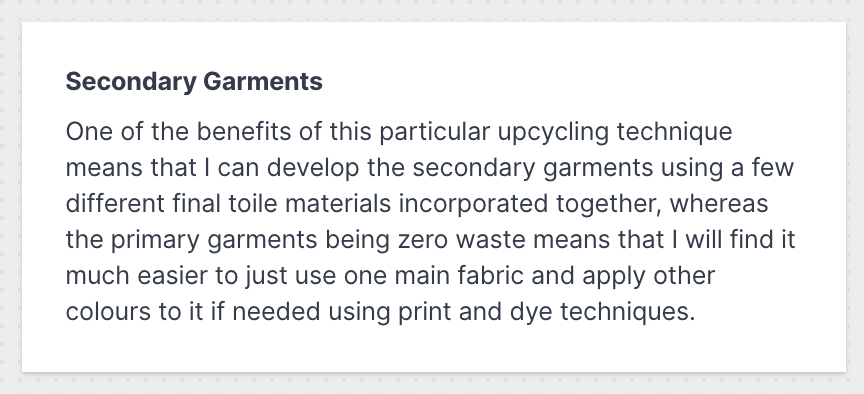
Debrief of Proposal and the Included Work
Skirt Toile

I found that working to create a garment based on a simplistic zero waste design approach (and having made a simple judgement call on weights of fabric, etc), and then better incorporating feature details and craft techniques worked out really well for me. In my previous zero waste work, the nuances of the concept of primary and secondary waste management meant that far too much of my time was taken up in patternmaking; and this was something I really wanted to avoid with this project. I think that even if I wasn't immediately entirely happy with the outcome of the design of the skirt, as a lot of it was designed through process, I was very happy with the good flow of application of technique and I think that now that I've started making, the design will begin to refine itself to a position where I'm really happy with.
I do intend to use a domestic machine to bind thread bound eyelet holes instead of having outstanding loops for lacing - I think this will make the back much cleaner whilst creating a sustainable alternative approach to using metal eyelets.

Bra Toile
I explained in my Proposal how I justified using the fabrics I did for this toile - the printed silk scraps were residual from my last semester minor project. I intend the final garment based on this bra to have the same print style and handcrafted buckle feature, but will instead use different subject matter aligning more with my life drawing and female nude theme.
My complaints about the fit of this garment (before any proper fittings, or only fitting on myself - size 12B) is that the placement of the buckle in the centre made the cups too far apart and therefore slightly ill fitting. My reasoning to designing the toile to fit my own size was so that it might be wearable, and because the B cup is generally a good mid-range standard size that I expect our fit models to be close to. I designed the back of the bra band to be fitted with a covered gathered flat elastic feature, so this measurement is very easily changed by model measurement and shouldn't need retoiling or refitting unless I significantly change design ideas. I think that it was absolutely worth constructing this toile to a high standard using proper finishings (and forgoing an earlier calico toile) because I've spent my semester break familiarising myself with these techniques and was most interested in toiling how the overall composition of the printed work of a technical lingerie piece would look in outcome, to check that my work based on this concept was moving in the right direction!
Further Design Developments
My ongoing design considerations lead me to think that every single primary garment needs to be converted into a secondary garment using final toile fabrics in order to fully justify sustainability and support the work contextually, which is why this design dev process is stretched out longer.
(This also requires consideration of fabric qualities and weight ranges for transferability to undergarments, upcycling of design lines and features, and
Note that with the problems of lockdown and lack of accessibility to fittings, right not it is best for me to focus on my primary garments, and to try to design them to be less fitted and more size flexible wherever possible - once I've finished toiling this work and have finalised models and been able to ascertain their sizes I'll begin to be able to start on the more fitted secondary garments. (Designing these on upcycled materials means the patterns aren't low waste and therefore I could grade them to be able to reproduce them to make the undergarments in my own size later after the project.)
Beading Scan
design idea


Lingerie - HOW Sustainable??
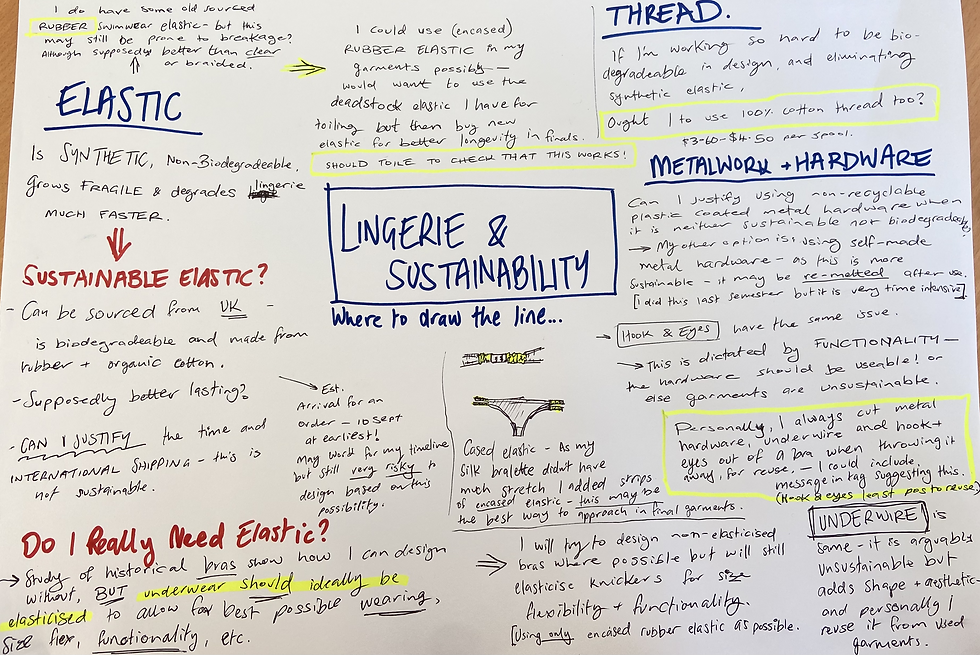
Primarily, clothing should be not only sustainable, but wearable...
Elastic
I started by considering the synthetics in bra elastic, and wondering if I could justify the use of such an unnatural product within a heavily sustainability based collection.
It is important for me to consider and decide on issues like this at early design stages, because technical decisions such as using elastic or not will impact the details and fit of the garment and thus impact my design decisions.
I first looked to see if there was any market for a sustainable elastic alternative. I found that some small UK based businesses do offer a GOTS certified cotton and rubber elastic as a biodegradable alternative. But, as explained above, I don't know that I can justify the environmental expense of shipping elastic all the way from the UK, and have no garantee that it would arrive in time. Some of these options are noted below:
Given that my collection is more sustainability process based, rather than organic certified fabric based (although I do intent to limit myself to strictly natural textiles and no elastane blends or equivalent), whether or not I wish to be absolutely strict in minding the different notions in the garments is something I'm deciding on now.
I also examined other existing products which claim to be environmentally minded: The Very Good Bra designs using sustainable elastic and textiles, and claims to be entirely 'circular minded', including custom made hook and eye pieces and tencel thread. Their ethics are explained as: 'We fundamentally believe that everything we make in the 21st Century should be designed with its end in sight. No excuses.'
As above, I then began to consider the function of elastic, whether it was necessary, and how it would behave if hoping to get a good amount of functionality, wear and durability out of a fashion artwork like the lingerie I'm intending to make. This excerpt from The Underpinning Museum examines a historical bandeau bra with early elastic which has been ruined by fragility and renders the garment unusable; which makes me feel as though the brittleness of elastic and the fact that it will degrade much faster than the rest of the garment means I ought to try to use it as least frequently as possible - particularly as I'm primarily using non-stretch woven materials like silk and thus it doesn't have the greatest range of functionality anyway.

My toile bra found the band elastics somewhat unnecessary, but did use larger strips of elastic in the back band as casing which allowed for the best range of flexibility. I feel that I will try to do this in future where possible: limit elastic a lot in bras. Knickers, on the other hand, do need a really good range of stretch so it's difficult to limit elastic.
I also considered a biodegradable alternative to synthetic woven elastic to be 100% rubber swimwear elastic. White rubber strip swimwear elastic has long been thought to be one of the best options as it is impervious to UV rays, water and salt. I do have a large amount of second hand rubber elastic to toile with; but this elastic does have something of a shelf life so I would definitely be best to purchase new elastic for my final garments.
In my sketch above I consider limiting elastic as much as possible, particularly in bras, and attaching elastic inside ruched fabric areas for best flexibility, in areas like the side of knickers and back of bras. Although I will reduce elastic as much as possible, and take inspiration to aid this from historical fashions, when I do need to add elastic I will do this with encased areas of 100% rubber elastic so as to be sustainable.
Places where I can locally source a new 100% rubber elastic for my final garments includes:
(Joann offers the most affordable cotton/rubber elastic I've been able to find, but this is still expensive and ships over from the US so I'm unsure I can justify the reasources?
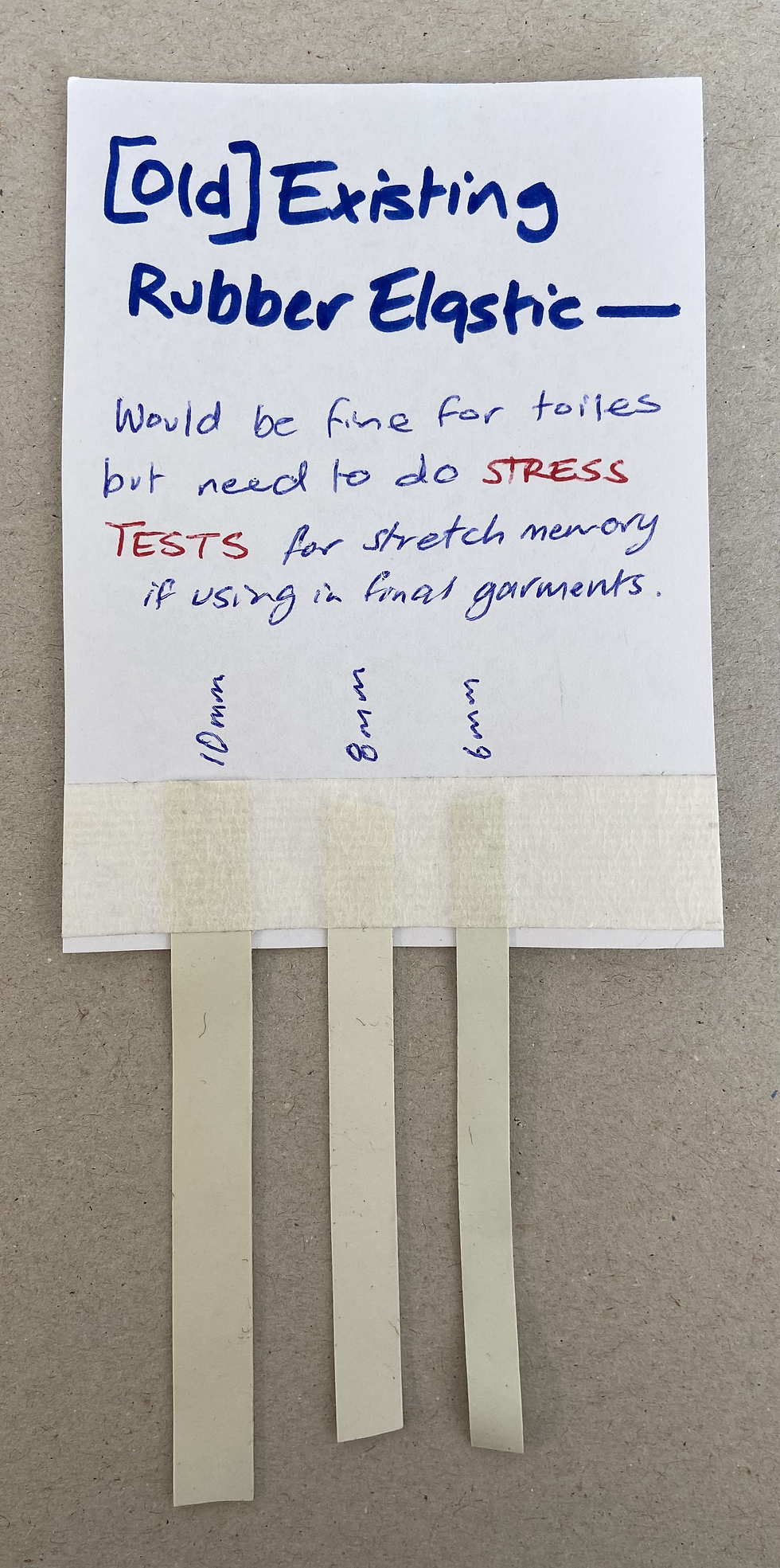
Either way, whether I decide to use synthetic elastic or not - I can know that cutting strips of a resource like this is zero waste in the production stage of a lifecycle, given that I only ever cut the exact amount I need to use. The reason drawing lines of sustainability like this is so difficult is because undergarments have a lot of other unnatural additives beyond elastic that I also have to decide on - these include underwire casing, underwire, metal hardware strap sliders, hook and eye back, any boning in corsets.
Hook and Eye Pieces, Metalwork Justification
[Considering Wearability]
I think a big question within my secondary collection is whether this hook and eye closure can be sustainable or not. Sustainability extends to the garments being as wearable and comfortable as they possibly can, as well as having ability for size to fluctuate, which the traditional hook and eye really allows for. At a base level, it should be important that my garments display good fit by fitting the models, who will likely have varying sizes.
In my past undergarments, I used other closures, like two adjustable handmade brass hook pieces in my tencel patchwork bralette, which was designed with no elastic and the inclusion of my own handcrafted metalwork pieces such as loops and sliders. However I do think that sustainability wise, I either need to include a functional hook and eye closure, or something equivalent to or better than this.
My question is whether I should incorporate traditional prefabricated bra hardware, including metal strap sliders and loops, and hook and eye closures; or whether I should fabricate these in my own metalwork explorations - they could be in brass, copper, silver, aluminum, etc.
The concept of creating in my own metal means that the hardware would not be either an alloy or have any type of coating - which would allow it to eventually be melted down and reused for something else or recycled as I (or another consumer?) so chose. However, this does divert a lot of time and energy that I may be better spent using in other areas of the project, and wouldn't be recommendable unless I could be absolutely sure that the handmade hardware would function just as well as conventional hardware. For reference, I made a lot of hook and eyes for a jeans fly in my last project, so handmaking a hook and eye band closure would be a possibility. I think that either way, a hook and eye could be preferable to other closure methods like ties.
Alternatively, in my toile bra I used conventional coated metal hardware for the back closure and strap sliders, but incorporated a handmade metalwork feature piece entirely from aluminum.
(Something I should really strongly consider and will need to test is the possibilities of corrosion or oxidisation of any metal I end up using! In my denim jeans I designed with copper specifically as it aligned with my historical research - but I did so with the knowledge that the metal would oxidise and tarnish through use, and this would add to the garment effect. Any other metalwork I use must be tested or incorporated deliberately as a design feature, or else the lifecycle of the garments may be compromised. (It may be possible that the metal I choose to use will need to be coated in a varnish poly coating to allow for durability, in which case this discussion would be moot.
I intend to discuss this issue with my lecturer - ought I to make my own bra hardware out of recyclable (and originally recycled) metal, or use recycled existing bra hardware metal pieces? - before coming to any final decision.
Something (as above) I always do is cutout areas of hardware before I throw a bra away, as I know I'll use them again. Adding this as a suggestion on the care tag is an option for these garments if I'm really wanting to incorporate conventional hardware, or even if I do use handmade metal pieces.
I should consider that bra underwire follows the same argument, but can also be similarly cut out of garments and reused, OR can be edited out of designs.
Historical Garments
I think that examining more historical approaches to things like sustainable bra closures may help me to determine some traditional and more sustainable ways to approach the issue - this aligns with my themes of both The Body in History, and The Body in Nature.
Historically, undergarments began with different varying formats of corsety, with underwear and bras not introduced until much later. Shapes and functions used to accentuate form included lacing (using thread bound eyelet holes, not metal), ties and overlapping or wrapping material.
I particularly like the function of the bathing corset, which wraps around the body through back holes to attach in an overlap at the front.
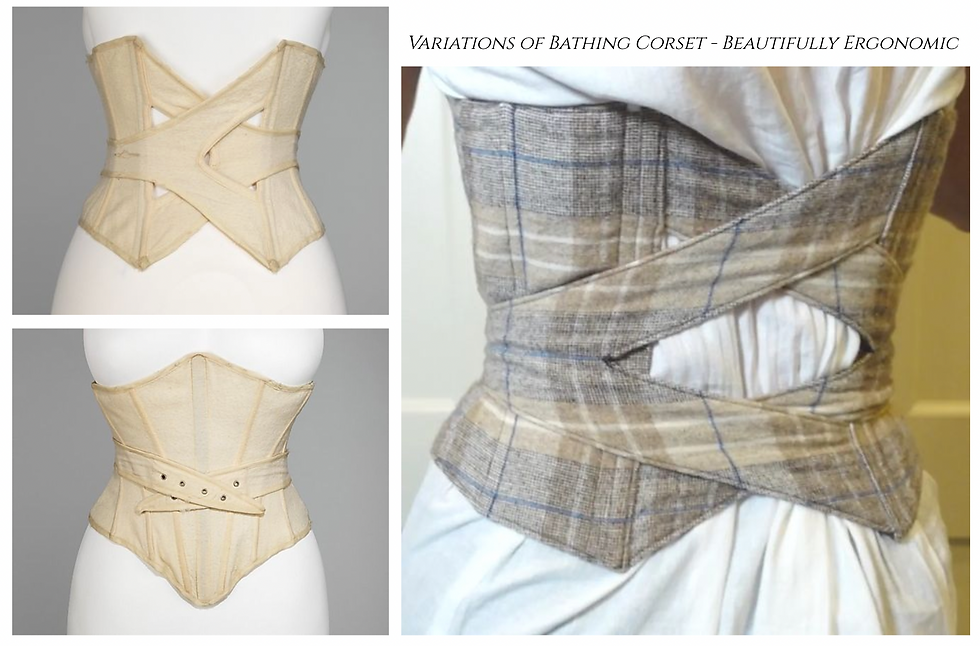
By the 1920's, fashions first began to change to find the accentuated and supported breast shape more flattering that the previous flattened and 'boyish' figure, as simultaneously health professionals began to examine women's and maternal health and campaign against breast flattening. In the 1930's, better size variation was developed and as the technologies and industry grew, elastic, adjustable straps, sized cups and padded bras were first developed.
I already incorporated techniques like the fan lacing into my first toile; adding handmade buckles. (Although some early versions I've seen bind the laces to fabric strips instead - that is less size flexible.) I must now being to strongly consider different elements of detail to be incorporated from a sustainability, functionality and size flexibility standpoint.
Longevity and Heirloom Clothing
One of the things that should be most important to me in my collection is that the clothing in wearable and built for longevity; structurally sound and constructed of quality materials and techniques; so that a beautifully made and sustainable garment may be treasured and worn for a very long time. Particularly as I'm incorporated printwork, as the garments moves more into an art piece than a utilitarian bra.
Threads
Arguably, if I'm making all of these considerations to biodegradable garments, I ought to use cotton thread in my garments? Most certainly for natural based (like silk) undergarments.
Denim Jacket - I'm very intent on making a denim jacket, but there isn't yet a manufactured alternative for denim thread that is 100% cotton, as the best recommended thread for durability is poly-cotton. Even sustainable denim brands like Nudie Jeans use coats poly-cotton thread because of this, as an heirloom garment must be durable and long-lasting! It does seem that I ought to use a best engineered product for my denim jacket, given that my most mindfulness is on the durability of the art piece and less so on the eventual disposal of it, as this is not an everyday-wear garment. However, there's nothing to stop me from being more ecofriendly and biodegradable by using cotton threads on the rest of the collection!
Existing Brands
I'd like to now acknowledge a sustainable lingerie brand which I admire and is significant to me - I did work experience on several photography shoots for Videris Lingerie this year, with designer Chloe Julian. I think that in regards to my big questions about what notions and hardware is and isn't sustainable, Videris's design approach is more based on sustainability in regards to our bodies, and how a more sustainable and natural based garment responds much better as a frequent wear item for the personal health of our skin.
(She also employs lots of theories about colour therapy, and delivers the lingerie in a range of bright colours in relation to psychological theory around mood.)
Videris uses a Tencel fabric given that this is not only more sustainable but also better for skin and moisture wicking. She does include elastane elastic in the products as they need to be very well elasticated in order to achieve really good fit for the highest levels of functionality and wearability. The fabrics used are OKO-tex 100 certified, meaning they've only been dyed with natural dyes. Videris bras don't use underwire (although some styles do use a centre u ring in the design), however this decision is much more centralised around brand ideals about lack of underwire and 'confinement' for women, than it is about reducing unsustainable metal pats in the undergarments.
(In my own garments, I'm working within the concept ideas of the female nude form being in confinement, comfort, beauty. Personally I think that using underwire really allows me to play around with these ideas of confinement but conform, shape and beauty; so it's something that I will still personally incorporate.
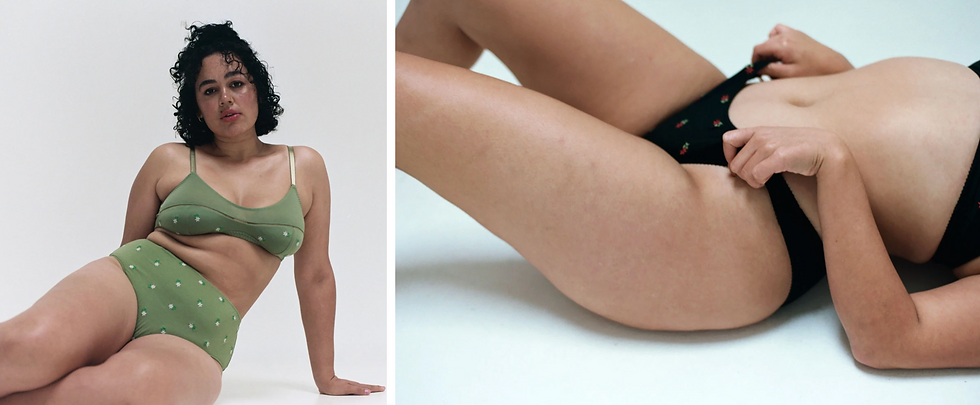

(I should definitely make a diagram like this for my own lingerie! This would be so fantastic to incorporate in the tag.)
Details and Considerations, Branding.


Note that I would also include on the tag about methods of biodegradability - eg. Cut off all of the metalwork, particularly in the Secondary Undergarments to make the garment biodegradable.

Approaching design for Zero Waste Denim Jacket
Image here of diagram and work notes
Birgitta Helmersson offers a purchasable zero waste workwear jacket - her particular version uses a square inserted shoulder, whereas I'm seeing others as being more fitted with a regular pieced together shoulder sleeve cap.
Comentários